Understanding the Role of an OEM CNC Lathe Part Supplier in Modern Manufacturing
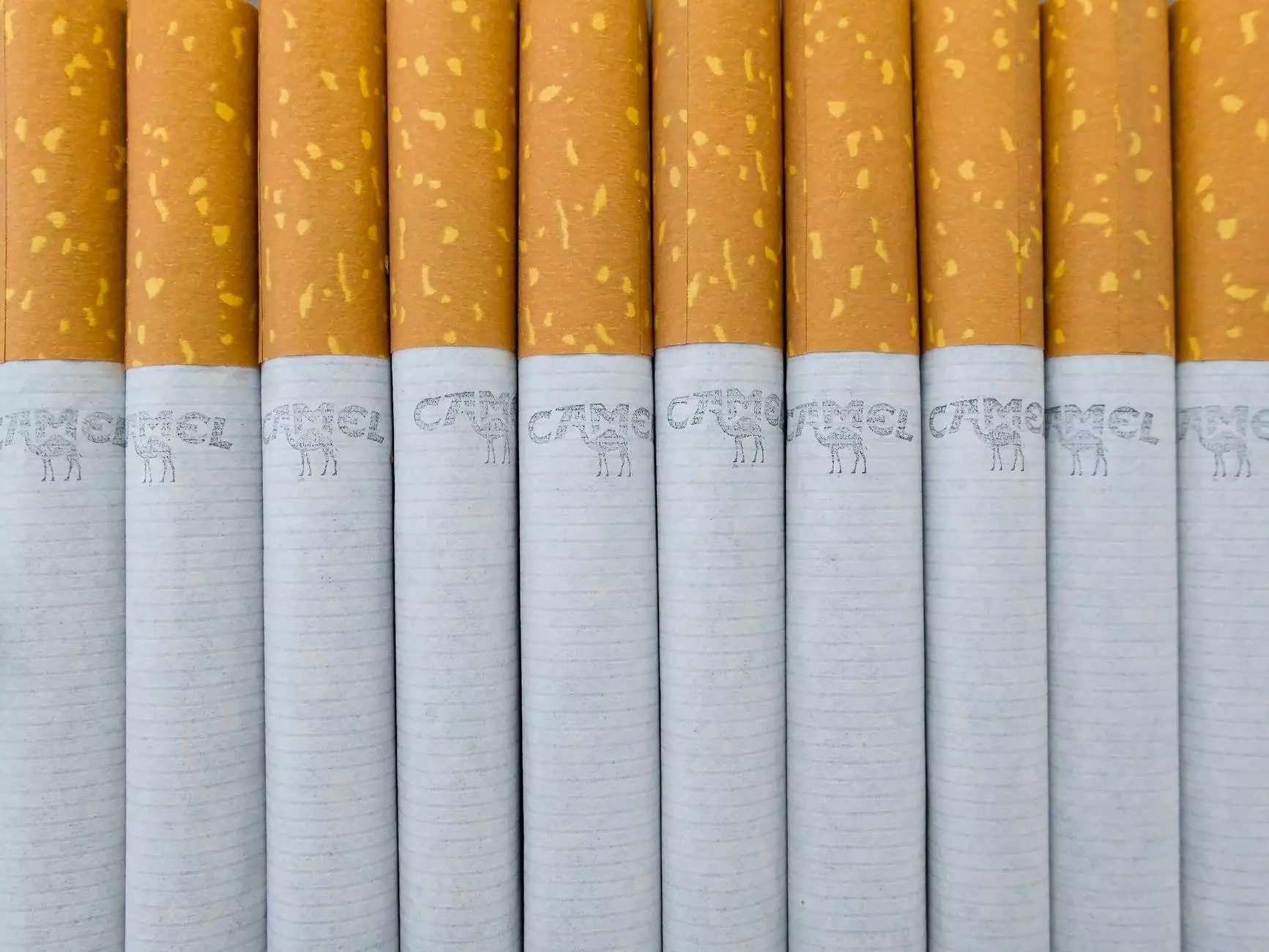
In today's competitive manufacturing landscape, precision and quality are paramount. Companies are continuously seeking ways to improve their production efficiency while maintaining high standards of quality. One critical aspect of achieving this goal is the role of an OEM CNC lathe part supplier. This article delves into the intricacies of this role, exploring not only what an OEM CNC lathe part supplier does but also why they are essential for businesses, especially within the realm of metal fabrication.
The Essentials of OEM CNC Lathe Parts
An OEM (Original Equipment Manufacturer) CNC (Computer Numerical Control) lathe part supplier provides precision components that are specifically designed and manufactured for particular machines or equipment. These parts are essential for various industries, including automotive, aerospace, medical devices, and machinery.
What is CNC Machining?
CNC machining is a subtractive manufacturing process highly regarded for its precision and efficiency. It employs computer-controlled machines to remove material from a workpiece, creating highly detailed and intricate designs that meet stringent specifications.
The Advantages of Using OEM Components
- Quality Assurance: OEM suppliers adhere to stringent quality standards, ensuring that each part meets the exact specifications required for optimal performance.
- Enhanced Performance: Parts designed specifically for a particular application offer better compatibility and efficiency, reducing wear and tear on machinery.
- Cost-Effectiveness: In the long run, using OEM parts can be more cost-effective due to their durability and reliability, which minimizes downtime and maintenance costs.
- Decreased Lead Times: Establishing a solid relationship with an OEM supplier can significantly reduce lead times for acquiring replacements or new components.
- Customization: An OEM CNC lathe part supplier can often provide customized solutions tailored to the specific needs and specifications of a business.
The Process of Working with an OEM CNC Lathe Part Supplier
Understanding how to effectively collaborate with an OEM CNC lathe part supplier can significantly impact your business operations. Below is a step-by-step guide to facilitate this relationship:
1. Identify Your Requirements
Before reaching out to a supplier, clearly define your needs. This includes the quantity, specific materials, tolerances, and any particular functionalities that the parts must meet. Such clarity will streamline communication and improve the outcomes.
2. Research and Select a Supplier
Not all suppliers are created equal. Research potential vendors by examining their expertise in metal fabrication, client reviews, and certifications. Websites like deepmould.net can provide insight into their capabilities and previous work.
3. Communicate Your Needs
Once you select a potential supplier, initiate a dialogue. Share your specifications, production timelines, and any constraints you may have. An experienced vendor will guide you on feasible solutions and adjustments that can be made to optimize production.
4. Prototype and Test
Many suppliers offer prototyping services. Creating a prototype allows you to assess the design and functionality of the part before committing to a full production run. Test the prototypes thoroughly to ensure they meet your requirements.
5. Place the Order
Once satisfied with the prototypes, place your order, ensuring that all communication regarding quantity, delivery schedules, and payment terms are clearly outlined. Keep an open line of communication throughout the production.
6. Evaluate Quality and Performance
Upon receiving your components, conduct thorough quality checks. Evaluate the performance of the parts in your systems and provide feedback to the supplier. This feedback loop enhances mutual trust and improves future orders.
Quality Control in CNC Lathe Parts Manufacturing
Quality control is a cornerstone of successful manufacturing, particularly for CNC lathe parts. An OEM CNC lathe part supplier implements rigorous quality assurance protocols, including:
1. Material Selection
Choosing the right materials is essential for durability and functionality. Suppliers typically source high-quality materials that meet industry standards, ensuring the finished product can withstand operational stresses.
2. Precision Machining Techniques
Utilizing advanced CNC machines ensures precision in every cut and finish. This precision results in parts that not only fit perfectly but also perform reliably within their intended applications.
3. Inspection and Testing
Before parts are shipped, they undergo comprehensive inspections and tests, including dimensional analysis and functional testing. This helps identify any defects early, ensuring only the best quality reaches the customer.
The Future of OEM CNC Lathe Part Supply
The future of the OEM CNC lathe part supply industry is evolving rapidly. Innovations in technology, materials, and processes continue to emerge, shaping how suppliers and manufacturers interact and function.
1. Embracing Automation and AI
As manufacturing moves towards greater automation, CNC machines integrated with AI and machine learning are anticipated to increase efficiency and reduce human error. Suppliers that adopt these technologies will likely command a significant competitive edge.
2. Sustainable Practices
With a growing focus on sustainability, OEM suppliers are increasingly seeking eco-friendly materials and practices. This shift not only meets consumer demand but also aligns with global trends pushing for reduced waste and responsibility.
3. Advanced Materials Engineering
The development of new materials, such as composites and alloys with enhanced properties, will expand the capabilities of CNC machining. Suppliers who invest in research and development will lead the charge toward creating lighter, stronger, and more versatile components.
Why Choose DeepMould as Your OEM CNC Lathe Part Supplier
When it comes to finding a reliable OEM CNC lathe part supplier, look no further than DeepMould. Here’s why:
- Expertise in Metal Fabrication: With extensive experience in the industry, DeepMould understands the nuances of metal fabrication, ensuring you receive the highest quality components.
- Customized Solutions: DeepMould prioritizes customer satisfaction, offering tailored solutions that meet your specific needs.
- State-of-the-Art Technology: Leveraging the latest CNC machining technologies, DeepMould ensures precision and quality in every part produced.
- Commitment to Quality: DeepMould’s rigorous quality control processes guarantee that you receive only the best parts for your manufacturing needs.
- Responsive Customer Service: DeepMould is committed to open communication, ensuring your queries and concerns are addressed promptly and efficiently.
Conclusion
In conclusion, partnering with an OEM CNC lathe part supplier is crucial for maintaining quality and efficiency in manufacturing processes. Suppliers like DeepMould are not just vendors; they are integral partners in the production journey. By leveraging their expertise, commitment to quality, and advanced technologies, businesses can achieve remarkable outcomes while staying ahead of the competition.
For businesses in need of high-quality, precision-engineered components, establishing a partnership with a trustworthy OEM CNC lathe part supplier is an invaluable investment for the future.