The Rise of **Lathe Parts Factories**: Revolutionizing Manufacturing
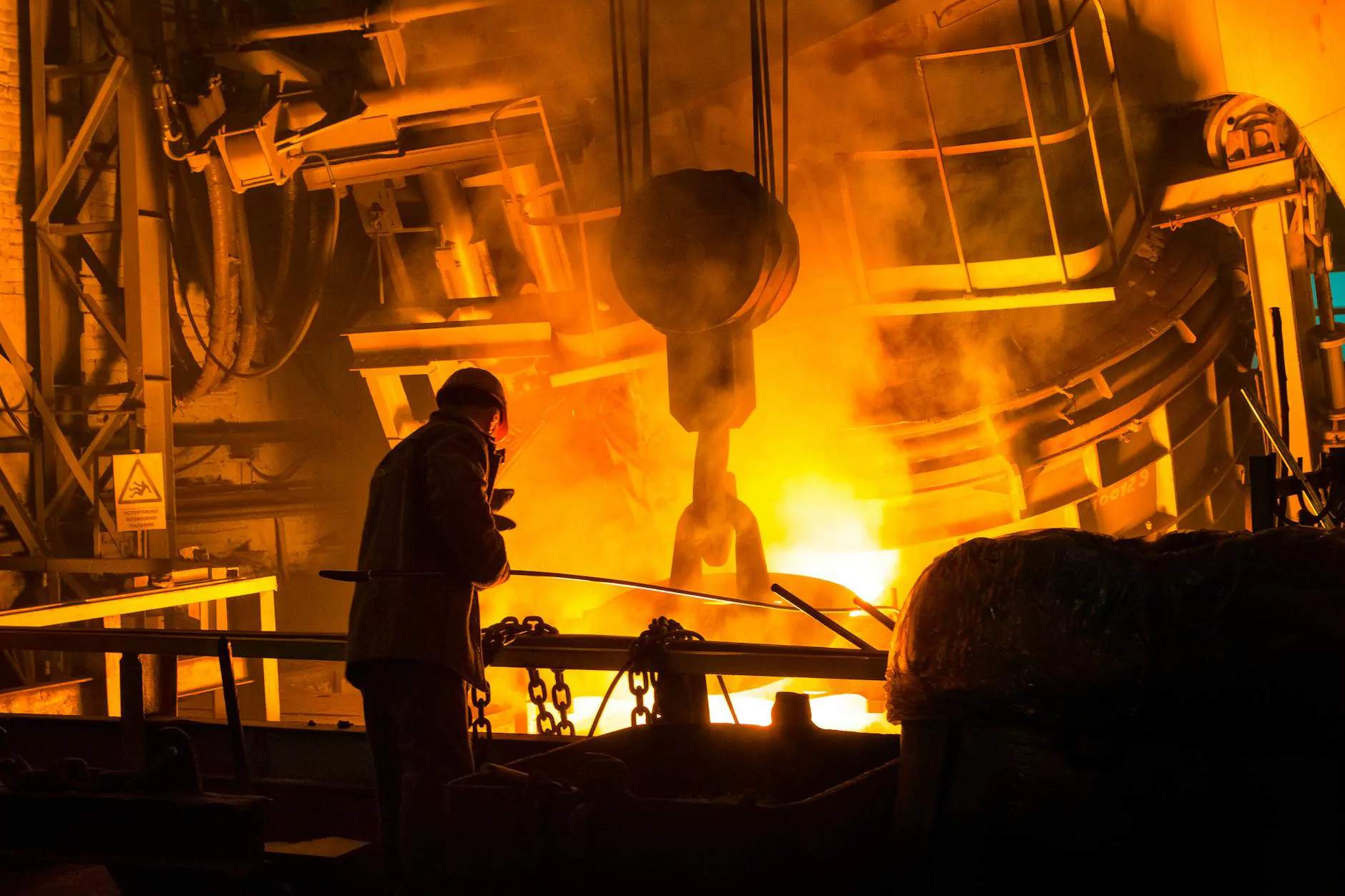
In an era where manufacturing precision and efficiency have taken center stage, the importance of lathe parts factories cannot be overstated. These specialized facilities play a critical role in producing high-quality components essential for various industrial applications. This article will delve into the significance of lathe parts factories, their operational processes, the tools they utilize, and the future landscape of manufacturing in this sector.
Understanding Lathe Machines and Their Parts
Before we explore the lathe parts factories, it is crucial to understand what a lathe machine is and its components. A lathe is a machine tool used for shaping, cutting, and machining materials such as metal, wood, and plastic. The accuracy of a lathe depends significantly on its parts, which may include:
- Spindle: The main rotating component that holds the workpiece.
- Tailstock: Located opposite the spindle, it provides support to the workpiece and can hold tools.
- Carriage: This part moves the cutting tool or workpiece during the machining process.
- Bed: It is the base of the lathe, providing stability and support to all other parts.
- Chuck: Clamps the workpiece to secure it during machining.
The Role of Lathe Parts Factories in Modern Manufacturing
Lathe parts factories are strategically significant in the manufacturing ecosystem for numerous reasons:
1. Precision Engineering
Factories that specialize in producing lathe parts adhere to strict quality standards. They utilize state-of-the-art machinery to ensure high precision and low tolerance levels in their parts. This precision is crucial in industries such as aerospace, automotive, and medical equipment manufacturing, where even the slightest error can lead to catastrophic failures.
2. Customization
One of the standout features of lathe parts factories is their ability to produce customized components tailored to specific requirements. This flexibility is achieved through advanced computer numerical control (CNC) technologies, allowing manufacturers to create bespoke solutions based on client specifications.
3. Cost-Efficiency
By streamlining production processes and optimizing material usage, lathe parts factories can reduce costs significantly. These savings are often passed on to the end-users, making high-quality components more accessible across various industries.
Key Processes in Lathe Parts Manufacturing
The production of lathe parts involves several critical processes, each contributing to the overall quality and efficiency of the final product.
1. Design and Prototyping
The manufacturing process begins with the design phase, where engineers create detailed CAD models of the components. Prototyping is then conducted to evaluate the design's functionality and make necessary adjustments.
2. Material Selection
Choosing the right materials is vital for ensuring the durability and performance of lathe parts. Common materials include various grades of steel, aluminum, and specialized alloys, each selected based on the intended application.
3. Machining Processes
Machining operations involve turning, milling, and drilling to shape the raw material into the final component. The lathe is the primary tool used in this phase, allowing for intricate designs and precise cuts.
4. Finishing
After machining, the parts undergo various finishing processes, including polishing, coating, and heat treatment. These processes enhance the surface quality, improve resistance to corrosion, and increase the longevity of the parts.
Challenges Faced by Lathe Parts Factories
Despite their vital contributions to the manufacturing sector, lathe parts factories encounter several challenges, including:
1. Technological Advancements
Keeping pace with rapid technological changes can be difficult. Factories need to continuously invest in training and upgrading their machinery to remain competitive.
2. Skilled Labor Shortage
The demand for skilled machinists and engineers is high, and factories often struggle to find qualified personnel. This shortage can hinder operational efficiency and impact production schedules.
3. Supply Chain Disruptions
Recent global events have highlighted the vulnerabilities in supply chains, affecting the availability of raw materials. Lathe parts factories must develop robust supply chain strategies to mitigate risks associated with material shortages.
The Future of Lathe Parts Factories
The landscape for lathe parts factories is evolving, with several trends shaping the future of manufacturing:
1. Automation and Robotics
Integrating automation and robotics into factories not only enhances efficiency but also improves precision. Automated lathes can operate continuously, producing parts with minimal human intervention.
2. Additive Manufacturing
3D printing and additive manufacturing techniques are increasingly being used alongside traditional machining methods. This hybrid approach allows for the production of complex geometries that would be difficult to achieve with conventional processes.
3. Sustainability Practices
With growing awareness of environmental issues, lathe parts factories are adopting more sustainable practices. This includes minimizing waste, recycling materials, and using energy-efficient machinery.
4. Data-Driven Decision Making
The rise of Industry 4.0 has ushered in an era of data analytics in manufacturing. Factories can now leverage real-time data to enhance productivity, predict maintenance needs, and streamline operations.
The Importance of Lathe Parts Factories in the Supply Chain
Lathe parts factories play an indispensable role in the broader manufacturing supply chain. Here are several reasons highlighting their significance:
1. Supporting Various Industries
From automotive to aerospace and beyond, nearly every industry requires reliable components produced by lathe parts factories. Their contributions are foundational to the functionality and safety of myriad products.
2. Ensuring Quality Standards
Lathe parts factories are committed to adhering to industry standards and regulations, ensuring that every part manufactured meets stringent quality criteria. This dedication to quality assurance fosters trust among clients and end-users.
3. Contributing to Economic Growth
As a crucial segment of the manufacturing sector, lathe parts factories attract investments, create jobs, and stimulate economic development within their regions.
Conclusion
In conclusion, lathe parts factories serve as the backbone of modern manufacturing, providing essential components that support a wide range of industries. Through their commitment to precision engineering, customization, and cost-efficiency, these factories are paving the way for a more robust and innovative future in the manufacturing landscape. As technology continues to evolve, so too will the capabilities of lathe parts factories, ensuring they remain a pivotal player in global manufacturing.
For more information on lathe parts manufacturing and to explore various metal fabrication services, visit deepmould.net.