Comprehensive Guide to Cutting and Welding Equipment: Unlocking the Power of Mini Arc Technology
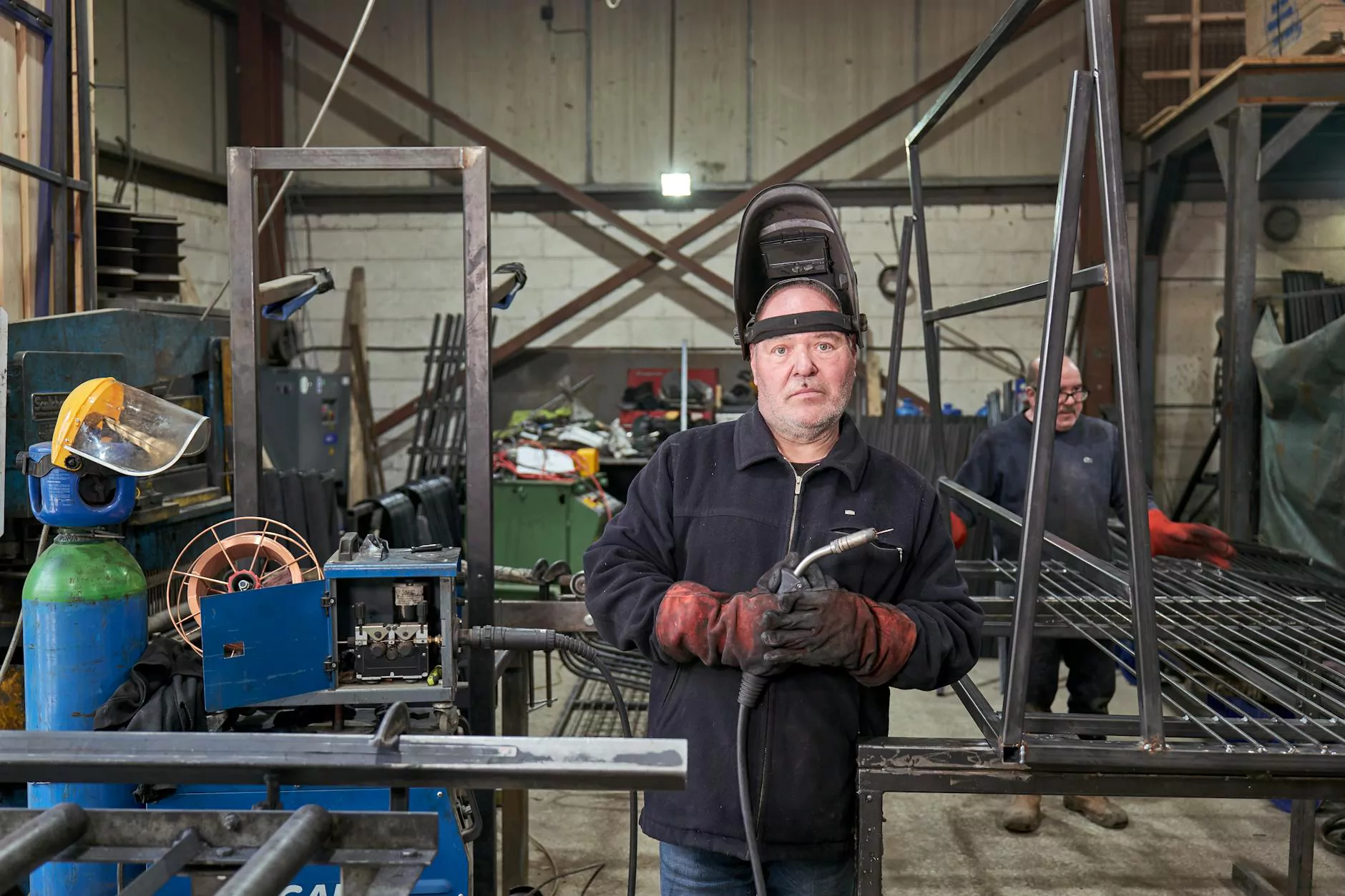
In the dynamic world of manufacturing, construction, and metalworking, the importance of cutting and welding equipment cannot be overstated. These tools form the backbone of countless industrial processes, enabling professionals to shape, join, and modify metals with precision and efficiency. Among the many advancements in this field, the advent of mini arc systems has revolutionized how artisans and technicians approach arc welding, offering unparalleled portability, control, and versatility. This comprehensive article offers an in-depth look into cutting and welding equipment, emphasizing the transformative role of mini arc technology, and providing actionable insights to optimize your operations.
Understanding Cutting and Welding Equipment: Foundations for Success
Effective metalworking hinges upon the right selection of cutting and welding tools. These instruments are designed to perform specific tasks, from slicing through steel sheets to creating strong, durable joints. The right equipment enhances productivity, ensures safety, and results in higher quality outcomes. Therefore, understanding the different types of equipment and their functionalities is essential for professionals aiming for excellence.
Types of Cutting Equipment
- Plasma Cutters: Use ionized gas to cut through conductive metals with high precision and speed.
- Oxy-Fuel Torches: Employ a mixture of oxygen and fuel gases for versatile cutting of ferrous and non-ferrous metals.
- Saws and Mechanical Cutters: Include band saws, cold saws, and abrasive cutting tools suited for thicker or specific materials.
Types of Welding Equipment
- MIG Welders: Use a continuous wire feed for efficient, high-speed welding, ideal for industrial applications.
- TIG Welders: Provide precise control, perfect for fine, detailed welds on thin materials.
- Stick Welders: Known for their robustness and ability to weld in challenging conditions.
- Mini Arc Systems: The focus of this guide, offering portability and high performance for versatile welding needs.
The Rise of Mini Arc Systems: A Game Changer in Welding Technology
Traditionally, arc welding required bulky equipment, extensive wiring, and a stationary work environment. This setup limited flexibility, especially in tight spaces or fieldwork applications. The evolution of mini arc systems addresses these limitations by delivering compact, lightweight, yet powerful welding solutions. These systems are ideally suited for both professional industrial use and DIY enthusiasts seeking quality without sacrificing mobility.
What is a Mini Arc System?
A mini arc system is a portable, lightweight welding unit designed to generate a stable arc with a minimal footprint. It incorporates advanced inverter technology, which enables high energy efficiency and consistent arc performance even with lower input power. These features make mini arc systems incredibly versatile, capable of performing in confined or challenging environments where traditional welding equipment would be impractical.
Advantages of Mini Arc Technology
- Portability: Compact size and lightweight design facilitate easy transportation and setup.
- Ease of Use: User-friendly interface with intuitive controls suitable for operators of all skill levels.
- Energy Efficiency: Reduced power consumption minimizes operational costs and supports sustainable practices.
- Versatility: Capable of welding a variety of metals, including steel, aluminum, and more.
- Precision and Control: Fine-tuned settings for meticulous welds on delicate or intricate components.
- Cost-Effectiveness: Lower equipment costs and maintenance requirements compared to traditional systems.
Applications of Mini Arc in Modern Industries
The lightweight nature and adaptability of mini arc systems make them invaluable across multiple sectors:
- Construction: Welding in confined spaces, on-site repairs, and structural fabrications where mobility is critical.
- Manufacturing: Precision welding in assembly lines, prototyping, and customization projects.
- Automotive: Body repairs, chassis modifications, and intricate vehicle customizations.
- Detail Work and Artistic Projects: Sculpting, metal arts, and jewelry making requiring delicate, detailed welding.
- Maintenance and Repair: Field repairs on heavy machinery, pipelines, and infrastructure components.
Choosing the Right Mini Arc System for Your Business
Selecting the optimal mini arc system hinges on understanding your specific needs. Factors such as welding capacity, power sources, portability, and compatibility with various metals should guide your choice. Here are some key considerations:
- Welding Thickness: Ensure the system can handle the maximum material thickness you will encounter.
- Power Supply: Compatibility with your available energy sources (e.g., single-phase, three-phase).
- Portability Needs: Weight and size considerations for mobile applications or confined workspaces.
- Electrode Compatibility: Support for different electrode types for diverse welding tasks.
- Ease of Maintenance: User-friendly design to minimize downtime and reduce operational costs.
- Additional Features: Digital controls, automated settings, or integrated cooling systems.
Integration of Mini Arc Systems with Cutting Equipment
To maximize productivity, it’s essential to integrate mini arc welding systems with complementary cutting tools. This combination streamlines workflows, reduces setup times, and enhances precision. For instance, pairing a mini arc welder with a portable plasma cutter can enable quick transitions between cutting and welding operations in field environments.
At tiendaguve.com, we offer a wide range of cutting and welding equipment designed to work seamlessly together, including mini arc systems, plasma cutters, oxy-fuel setups, and more. Our curated selection ensures your business has access to the highest quality tools for demanding industrial applications.
Maintaining and Extending the Lifespan of Your Mini Arc Equipment
Proper maintenance is crucial in ensuring that your mini arc systems perform optimally throughout their lifespan. Regular inspection, cleaning, and calibration prevent unexpected breakdowns and maintain weld quality. Some best practices include:
- Cleaning the gun and cable connections after each use to prevent dirt and debris buildup.
- Checking for wear and tear on consumables like electrodes and contact tips.
- Storing equipment in a dry, dust-free environment to prevent corrosion.
- Following manufacturer-recommended maintenance schedules for internal components.
- Updating firmware or control software when available for enhanced performance.
The Future of Cutting and Welding: Embracing Innovation with Mini Arc
As technology continues to advance, mini arc systems are expected to become even more sophisticated, integrating features like wireless controls, smart diagnostics, and AI-assisted welding. These innovations will further empower professionals to work more efficiently, safely, and precisely. Embracing these emerging trends ensures your business remains competitive and at the forefront of industrial innovation.
Partnering with tiendaguve.com
At tiendaguve.com, we specialize in providing high-end cutting and welding equipment, including the latest mini arc systems tailored for diverse industrial needs. Our team of experts is committed to guiding you in selecting the ideal solutions to optimize your workflow, enhance safety, and reduce operational costs. With our extensive inventory, competitive prices, and dedicated customer support, we ensure your success every step of the way.
Conclusion: Elevate Your Metalworking with the Power of Mini Arc Systems
The evolution of cutting and welding equipment has opened new horizons for industry professionals seeking portability, efficiency, and precision. Among these technological marvels, mini arc systems stand out as a transformative tool that can redefine your approach to metal fabrication, repair, and artistic endeavors. By investing in the right mini arc solution and adhering to best practices, you ensure your operations are safer, faster, and more cost-effective. Embrace the future of welding — leverage the power of mini arc and stay ahead in the competitive landscape.