Rapid Injection Molding Prototyping: Transforming Metal Fabrication
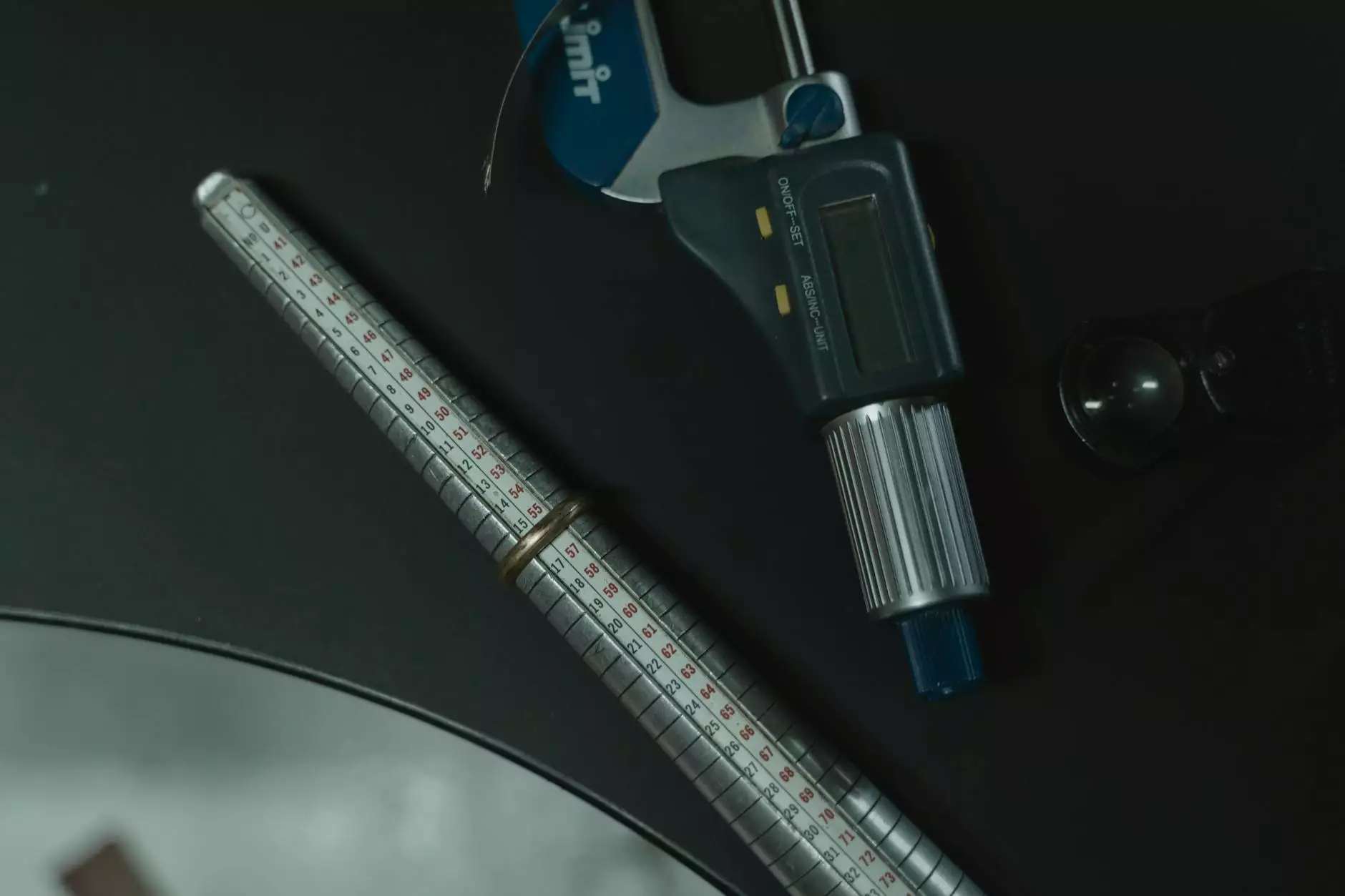
In a world where innovation is the key driver of business success, manufacturers are increasingly relying on advanced techniques such as rapid injection molding prototyping to streamline their processes, enhance product quality, and reduce time to market. This article will delve deeply into the myriad benefits of this technology, its applications, and why it stands out as a game-changer in the field of metal fabrication.
Understanding Rapid Injection Molding Prototyping
Rapid injection molding prototyping is a highly efficient manufacturing technique that allows for the quick production of prototype parts using injection molding techniques. This method significantly reduces the time and cost associated with traditional prototyping methods. By utilizing soft tooling and advanced 3D printing technologies, manufacturers can create molds quickly and produce high-quality parts in a fraction of the time.
The Process of Rapid Injection Molding
The process involves several key steps:
- Design: The initial phase starts with a detailed design phase, where CAD (Computer-Aided Design) software is used to create part designs that are ready for prototyping.
- Tooling: In this stage, manufacturers create molds using soft tooling materials such as aluminum or 3D-printed mold inserts, which are comparatively quicker and cheaper than traditional hard tooling.
- Injection: The molten material is injected into the molds. This can be done using a variety of materials, including thermoplastics, which are frequently used in injection molding.
- Cooling: The injected material is then cooled to solidify it, after which the mold is opened to retrieve the prototype.
- Finishing: Finally, the prototype may undergo additional processes such as sanding, painting, or coating to achieve the desired finish.
Advantages of Rapid Injection Molding Prototyping
The adoption of rapid injection molding prototyping comes with numerous advantages that make it a preferred choice for businesses in the metal fabrication sector:
1. Reduced Lead Times
The most apparent benefit of rapid injection molding prototyping is the significantly reduced lead times. Traditional prototyping methods can take weeks or even months to complete. However, with rapid prototyping, manufacturers can create and test prototype parts within days, allowing for faster iteration and quicker market access.
2. Cost-Effectiveness
By utilizing soft tooling and advanced technologies, companies can significantly cut down on production costs. These molds are quicker and cheaper to produce, providing companies with a more affordable solution for prototyping compared to the conventional methods.
3. High Precision and Quality
Rapid injection molding prototyping does not compromise on quality. The technology allows for the production of precise, high-quality parts that are highly representative of the final product. This high level of accuracy is crucial for ensuring that prototypes perform adequately during testing.
4. Flexibility in Design
This method allows for easy adjustments and modifications. Designers can quickly implement changes to the CAD design based on testing feedback, enhancing the overall design and functionality of the product. This flexibility ensures that businesses can innovate rapidly without incurring excessive costs.
5. Material Versatility
Rapid injection molding supports a wide variety of materials. From thermoplastics to elastomers and even some metals, manufacturers can choose the most appropriate materials that suit their prototype’s functional requirements and end-use applications.
Applications of Rapid Injection Molding Prototyping
The applications of rapid injection molding prototyping span various industries. Here are some key sectors utilizing this technology effectively:
1. Automotive Industry
The automotive industry has heavily invested in rapid injection molding prototyping for developing parts such as dashboards, panels, and other components that require precision. This technique allows for quick testing of designs, ensuring that they meet safety and performance standards before full-scale production.
2. Consumer Electronics
In the tech world, where products evolve rapidly, the ability to prototype and test components like casings, connectors, and internal structures through rapid injection molding is invaluable. It allows electronic manufacturers to stay ahead of the competition.
3. Medical Devices
Medical device manufacturers require stringent quality and adherence to regulatory standards. Rapid injection molding supports the production of prototype devices or components that are both safe and reliable, streamlining the path to compliance and market release.
4. Aerospace Sector
In aerospace, where precision engineering is critical, rapid injection molding prototyping supports the development of lightweight, high-strength components that meet the rigorous demands of this industry.
5. Consumer Goods
The consumer goods industry is seeing rapid integration of this prototyping process, allowing for quick development cycles of products ranging from household items to sports equipment, ensuring they meet customer expectations without unnecessary delays.
Why Choose DeepMould.net for Rapid Injection Molding Prototyping?
At DeepMould.net, we understand the complexities involved in the metal fabrication industry and the need for rapid, efficient solutions. Our rapid injection molding prototyping services are designed to meet the evolving needs of our clients, providing them with high-quality prototypes at an unmatched speed. Here’s why you should choose us:
1. Expertise in Metal Fabrication
With years of experience in the metal fabrication industry, our team brings extensive knowledge and expertise to every project. We understand the materials, processes, and regulations involved, ensuring that your prototypes not only meet designs but also comprehensive industry standards.
2. Advanced Technology
We leverage state-of-the-art technology, including 3D printing and advanced molding techniques, to deliver high-precision parts that align closely with your specifications. Our commitment to investing in technology enables us to offer you the best capabilities available in the market.
3. Customer-Centric Approach
At DeepMould.net, our clients are our priority. We work closely with you throughout the prototyping process, ensuring that your feedback is incorporated at every stage for optimal results. Our aim is to provide a transparent, engaging, and collaborative service that enhances your experience.
4. Quick Turnaround Times
We pride ourselves on our ability to deliver prototypes faster than traditional methods, allowing you to focus on what matters most: your project’s success. Our swift turnaround times mean that you can iterate, test, and launch new products rapidly.
5. Competitive Pricing
We believe that quality doesn't have to come at a premium. Our competitive pricing structures reflect our commitment to providing exceptional value without compromising on quality. By choosing DeepMould.net, you get high-end quality at accessible price points.
The Future of Rapid Injection Molding Prototyping
The landscape of manufacturing is continuously evolving, and the adoption of rapid injection molding prototyping is set to grow exponentially. As technologies advance, we expect to see even greater improvements in efficiency, speed, and the types of materials that can be utilized.
Emerging Trends to Watch
- Increased Adoption of Automation: Automation technologies are poised to enhance the efficiency of rapid injection molding processes, reducing human error and enhancing consistency.
- 3D Printing Integration: The combination of traditional injection molding processes with advanced 3D printing technologies will continue to create hybrid solutions that improve prototyping speeds and capabilities.
- Sustainability Focus: The drive for sustainable manufacturing practices will encourage the use of eco-friendly materials and processes in rapid injection molding, reflecting industry trends towards sustainability.
- Enhanced Software Tools: Advances in design and simulation software will provide even better capabilities for designers and engineers to predict performance outcomes and optimize designs before physical prototyping.
Conclusion
In conclusion, rapid injection molding prototyping is revolutionizing the metal fabrication industry, unlocking new efficiencies and opportunities for innovation. With benefits ranging from reduced lead times and cost savings to high precision and flexibility, this method is transforming how companies approach product development. By choosing experts like DeepMould.net, businesses can ensure they remain at the forefront of their industries, leveraging cutting-edge technologies and practices to achieve their goals.
Investing in rapid injection molding prototyping is not just a smart move; it is a strategic necessity in today’s competitive landscape. As we move into the future, the potential for this technology will only continue to expand, setting the stage for unparalleled advancements in product design and manufacturing excellence.